Ten Key Stages of Modular Construction
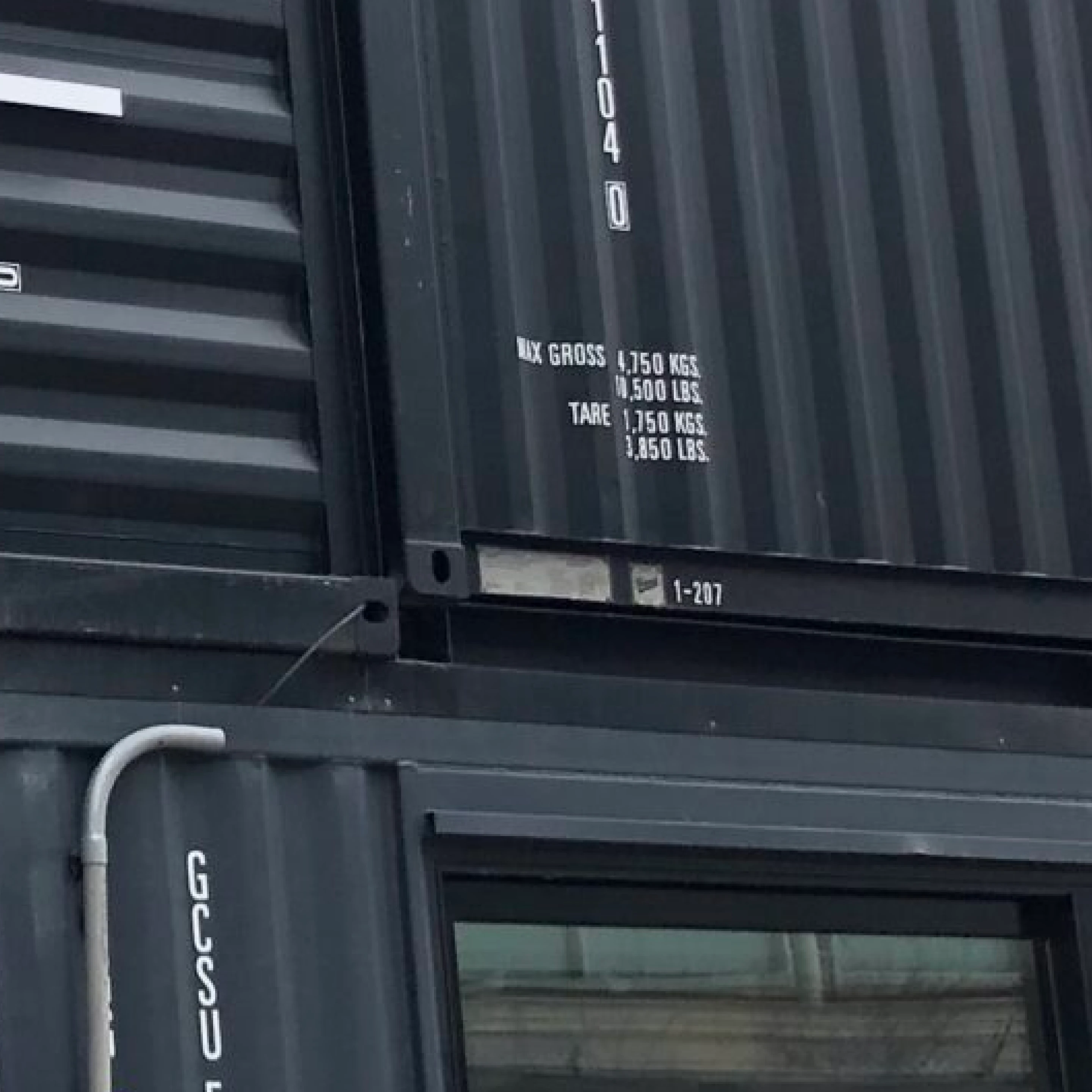
Our shipping container fabrication process follows a strict regimen of rules and regulations to ensure safety in structural integrity and Giant quality. Business, personal, or experiential, Giant Containers works to optimize your projects’ quality and cost.
Read on to learn more about the Ten ‘Key Stages’ of modular construction.
1. Budget
Modular and prefabricated buildings require funding distributed throughout the phases of design and construction. Our knowledgeable sales team works with you to refine concepts and provide estimates based on project size and complexity. As the project progresses through the design phase, a more accurate contract cost is going to developed and agreed upon with the finalization of design.
2. Design
Our in-house designers can turn your concepts to reality, or adapt your existing drawings to modular fabrication plans. We have built containers to top frigid ski-resort Mountains, and to withstand tropical climates. We can design containers suited to your needs. Municipal regulations and local construction by-laws must be defined during design to avoid any potential delays or illegalities.
3. Scope of Work
Large modular projects are often split into two scopes. Giant Containers focuses on the fabrication and delivery of the container modules, a General Contractor is often required for assembly/installation of structure, finishing sub-trades, site permits/prep etc. Depending on the size and complexity of the project, it is possible for clients to be their own general contractor. Over the years Giant Containers has compiled a Directory of Reputable Contractors operating throughout various locations in North America to aid our clients in finding experienced workers. It is important source contractors who have worked with modular containers as their steel frames can require different installation methods than wood and concrete enclosures.
4. Site Permits/Prep
As with any project, modular installers must obtain site specific permits prior to construction. The Giant Team is experienced in guiding clients through modular project planning, but ultimately it is the responsibility of the Client or General Contractor to acquire all necessary permits for the project prior to construction.
Land preparations and foundation requirements are dependent on project size and intended use. While modular containers are robust in design - site clearing, grading, and proper foundation is going to extend the structural integrity of containers. Research should be done to ensure access to local city services such as hydro and sewer are available at your site. It is also important to consider install methodology while preparing your site e.g. crane set-up location, flatbed delivery route.
5. Production
This is the "Finish" phase of your project! Operating out of two fabrication warehouses, one geared for large scale projects and the other for specialized custom work – Giant Containers is going to materialize your designed container modules with great quality, and efficiency.
Main stages of production:
- Main Assembly
- Custom Cut-outs
- Steel Structure Welding
- Steel Studding
- Spray Foam Insulation
- Painting
- Windows and Flooring
- Finishing Line
- Inspection
For more details on how we take your project from the main assembly to the finishing line, download our overview deck.
6. Delivery
Once the containers have passed our quality inspection and are ready for delivery, our team is going to arrange overseas shipping and, if required, can help arrange transport right to site. The containers arrive on flat beds and we work together to determine the best order of arrival.
Large scale projects shipping overseas generally require 3-5 weeks from factory to your closest port. Transportation from port to site is done by train and/or trucking – depending on location, generally 1-2 weeks. Location tracking updates are available throughout the shipping process to accurately coordinate arrival activities. To help ensure the delivery of the containers goes smoothly, one of our team members is going to be on-site with you to supervise and assist.
7. Installation
Structure assembly is where you are going to notice the huge advantages of Modular Container structures. With proper site preparation and staging for cranes/trucks, going from delivery to a standing structure can often be completed in just days. The general contractor should utilize on-site welders to configure and secure ground level containers to the foundation. From there, additional levels can be attached via twist locks very quickly.
8. Subcontractors
Once your structure is assembled and secured it’s time to bring in your subcontractors. Carefully managing the sequence of your electrical, plumbing, HVAC, and finishing trades, is important to ensuring your install runs smoothly. Giant’s diverse project experience and close relationship with past clients allows us to provide knowledgeable consultation when required for you or your General Contractor.
9. Weatherproofing
Container modules structures are robust in nature and with proper weatherproofing. We recommend working with a roofing contractor to seal areas where water can pool e.g. between stacked containers, ground-level containers and foundation and on top of the structure. There are many options for roofing and Giant can provide examples of past projects with traditional or HDPE membrane roofing to help you conceptualize your finish.
10. Connections to Services
When your electrical, plumbing and HVAC subcontractors are complete you need local inspectors to certify their work and issue connection permits to city services. Once you’re hooked up and the finishing subcontractors are done, it’s time to move in!
Enjoy your New Modular Container Building!
Need some more inspiration?
Check out our recent projects
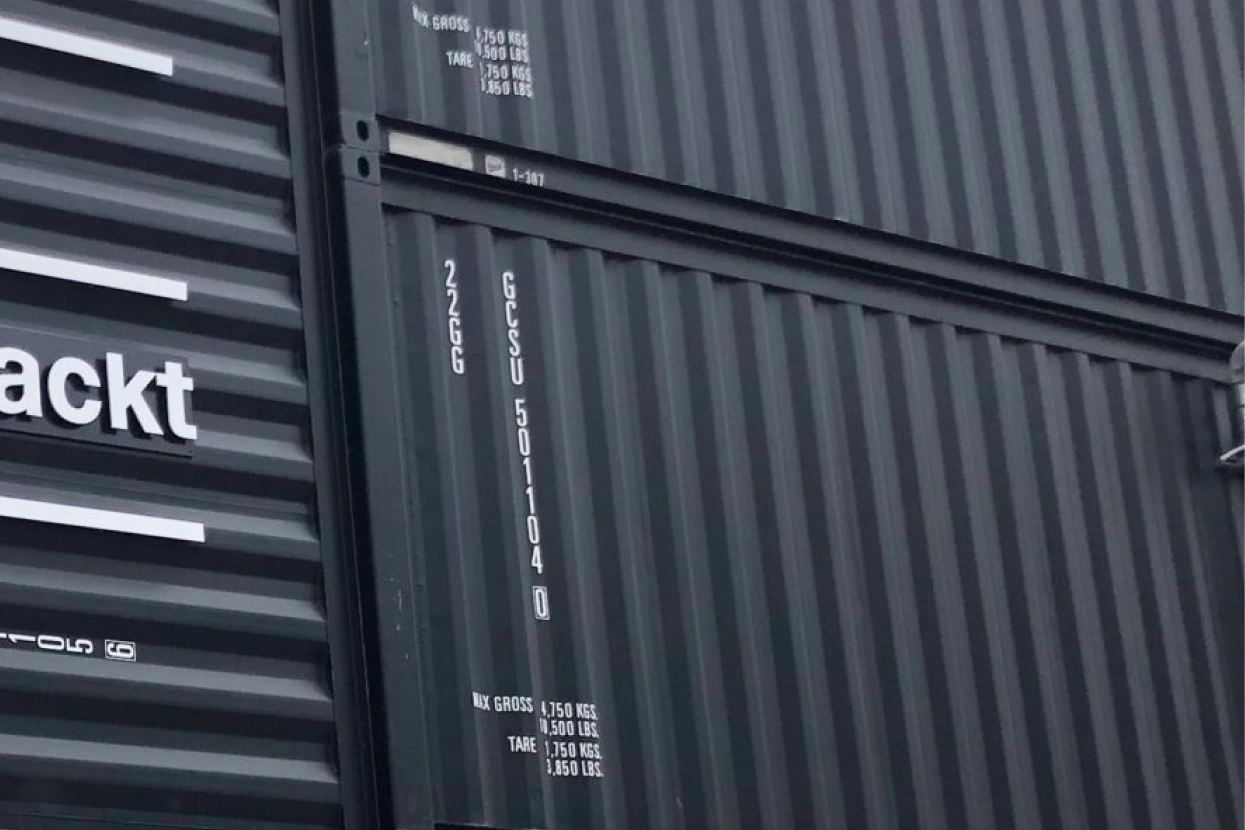